Covering Embodied Carbon Series
Covering Embodied Carbon: what do I do about it?
Read Time 7 mins | Written by: Alex Bantock
TL;DR
- There is no silver bullet for reducing embodied carbon in buildings as buildings and their associated emissions are context-dependent
- The World Green Building Council’s (WGBC) guiding principles for a sustainable building include: build nothing, build less, build clever, build efficiently, minimise waste, and offset residual emissions
- Time and measurement are essential in reducing embodied carbon
We know what embodied carbon is, why we should care about it, and how to measure it - but now it’s time for the most important part: reducing it. The Dutch Green Building Council’s (DGBC) ‘Paris Proof Commitment’ was introduced in an effort to make urban buildings more sustainable so that we can reach the Paris Agreement goal (i.e. to limit global warming to well below 2, preferably to 1.5 degrees Celsius, compared to pre-industrial levels). In order to achieve the Paris Agreement, the built environment can only use the limited carbon apportioned to it - which includes energy and material resources. Therefore, the Paris Proof Commitment dictates that buildings must be (re)designed to use no more than one-third of current energy consumption and have a 50% reduction in baseline emissions by 2030. The UK Green Building Council (UKGBC) has followed suit setting similar targets so that the UK economy can achieve its net zero emissions by 2050 target. This poses a challenging task given that approximately half of all building emissions will be embodied by 2040 . Therefore, embodied carbon in the built environment is an extremely important focus point going forward and we should be making every effort to reduce it on an industry-wide level.
Reducing embodied carbon is context-dependent
First off, it is important to know that there is no silver bullet when it comes to low-carbon, net-zero carbon, or zero carbon buildings. This is because buildings are very much context-dependent: they interact with their environment, often depend on local resources, and are subject to different weather conditions and natural disasters. For example, the sudden uptake in timber construction is due to timber being considered the ‘greenest’ construction material that allows for fast-paced development (sounds perfect right?). However, the environmental benefits of timber are often misconceptions, as timber is only truly ‘sustainable’ if it is locally sourced from a forest that is sustainably managed. Otherwise, logging can result in deforestation and destruction of critical conservation areas and transportation over large distances negates majority of the carbon savings.
Biomass materials are also accompanied by carbon accounting issues, with the ongoing debate of whether to include biogenic carbon in life cycle assessments or not resulting in skewed LCA results and EPD values (for the sake of brevity this will be discussed in a later blog post). Nevertheless, whilst there is no single recipe for achieving low- to zero-carbon buildings, there are a few universal guidelines that can help.
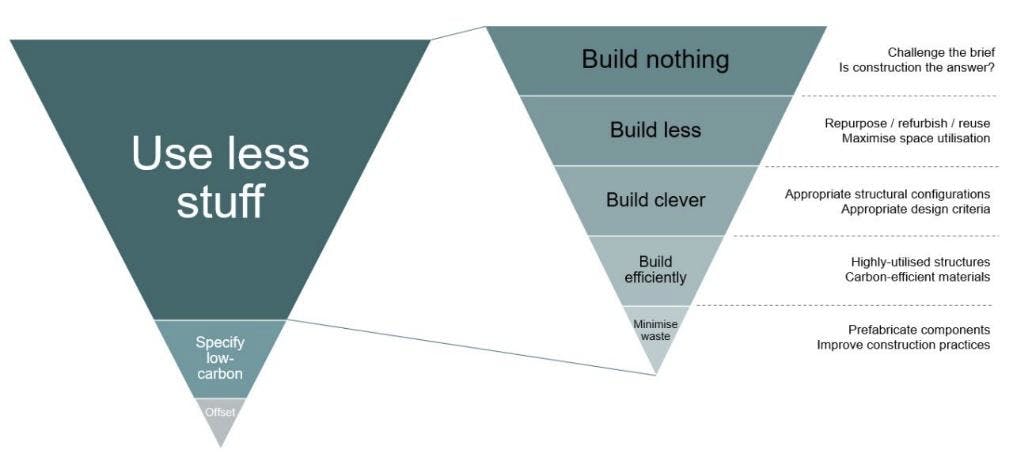
See source: WGBC - Bringing Embodied Carbon Upfront
The World Green Building Council’s (WGBC) inverted triangle illustrates the guiding principles for a sustainable building in order of their priority. The key message is to “use less stuff” by building nothing, building less, building clever, building efficiently, and minimising waste:
- Build nothing: When looking at existing buildings, the three magic words are retain, retain, retain. Think critically as to whether building more or building new is the answer. Do we need to use new materials at all? Remember that building nothing eliminates the potential for embodied carbon emissions.
- Build less: Can we still achieve improved functionality by utilising existing assets via renovation or reuse? Are there creative ways that we can repurpose the existing space?
- Build clever: If building new, ensure that you are making the right design choices by using low-carbon design guidance and carbon calculation tools and benchmarks. Whole Life Carbon Analysis is important in ensuring that further steps and decisions are well-justified.
- Build efficiently: Mitigate upfront carbon emissions by minimising the need for new materials and prioritising sustainable materials (low-impact materials or materials with a high-recycled content) and construction techniques. Materials and components that are likely to be high in embodied carbon include CEM1 cement (100% Portland cement), aluminium, and reinforced steel. Be sure to also consider the future use scenarios and end of life of the building, where possible, to allow for future adaptation and disassembly/deconstruction for reuse/recycling.
- Minimise waste: Minimise construction waste through prefabrication, efficient design, ensuring the appropriate quantity and size of materials are ordered, storing materials properly, reusing and recycling materials, and using optimised and energy-efficient construction techniques.
- Offset residual emissions: Offset any residual carbon emissions within the project boundary or by using a verified offset scheme. Note that offsetting emissions is an absolute last resort and should not be considered earlier than any of the above steps.
Use guidelines, standards, and certification requirements to guide you
Whilst these principles provide some insight into what sort of actions to take, following a set methodology of some sort will always result in a more efficient design and build. Luckily, more and more organisations are releasing guides and standards, many of which echo and expand upon the above principles. For example, in the UK, LETI’s Climate Emergency Design Guide and Embodied Carbon Primer are straightforward and informative documents outlining how to design low-impact and low-embodied carbon buildings. The RICS Whole life carbon assessment for the built environment sets out mandatory requirements, expectations, and recommendations for best practice in whole life carbon assessment in buildings. And the RIBA Plan of Work provides guidance on briefing, designing, constructing and operating building projects to ensure that building projects factor in all technical requirements and procedures in the most efficient manner. There are a number of similar regulations, standards, certification systems, and guides around the world, and recommendations can often be widely applicable and used globally.
Stay tuned for our The Embodied Carbon Landscape series.
Remember that time is not your friend when it comes to embodied carbon
Critical to all of these principles and guides are the components of time and measurement - the sayings “it’s better late than never” and “what you don’t know won’t hurt you” definitely do not apply well to reducing embodied carbon in buildings. This is because addressing embodied carbon too late in the project often means it can not and will never be reduced. In addition, accurate measurement and data are critical to carbon mitigation - without reliable data, we cannot produce the most efficient designs and identify carbon hotspots for reduction. Remember that the bulk of embodied carbon emissions are emitted during the product and construction stages (i.e. upfront embodied carbon), so our ability to reduce them is restricted to the short planning and design window in the project development stages. If you would like to know how Preoptima can be used at the earliest conceptual stages of design right through the entire building lifecycle, contact us at info@preoptima.com.
See our Covering Embodied Carbon: when can I reduce it? blog post to discover when you have the greatest carbon reduction potential.
We'd love to hear from you!